Instructions on usage of hybrids.
How to use packaging.
The liners are attached to the filling head of the aseptic filling machine which sterilises the specialised filling gland before penetrating the seal and allowing sterile product t enter the bag. Once the bag has achieved the correct weight the flow is switched off and the filling machine flushes the inlet with 140 steam prior to heat sealing the filling gland.
Top of internal liner (under lid of IBC) showing heat sealed filling nozzle which must not be opened for any purpose.
No attempt should be made to open the liner at the top inlet as this will leave the contents exposed to atmosphere and as such they must be used within 48 hours.
Removing the plate
- The front of the valve will be protected from accidental forklift damage by a ply-board cover secured with 2 * stainless screws.
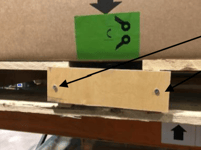
- Remove the screws and the plate to reveal the valve.
-
- If the plate is missing on arrival, check the outlet valve for signs of damage including an inspection of the (blue or black) dust cap which should be connected to the valve top and bottom by a small tamper evident plastic tie.
Note: If damaged use the link below to find out how to correctly report damage.
https://knowledge.puremalt.com/en/knowledge/guide-to-photographing-evidence-for-complaints
Removing tamper evident dust cap
- Remove tamper evident dust cap from valve by unscrewing and make sure that there is no product behind the dust cap. If product has leaked through the valve it should be reported.
Report - The above image is showing valve with dust cap in position - Handle pointing down means it is closed.
- The above image is showing the dust cap removed and valve closed and clean.
- The valve cannot be opened with the Dust Cap in position, trying to do this will result in damage to the valve or valve handle.
Using the product (valve)
- The bag should only be opened using the bottom valve as this precludes contaminated air from entering the bag on the principle that as product exits the bag the internal liner collapses. To open the valve the valve should be pushed through 90° upwards.
- The integrated valve on these bags is made from polyethylene and will not stand up to the rigours of constantly opening and closing in the manner of a steel valve. Therefore, if the method of utilisation requires this a stainless steel valve must be fitted in line and preferably directly onto the plastic valve or as close as possible. This valve should then be used as the main shut-off and the plastic valve left open.
- Continual use of the plastic valve may lead to failure of the seal and leakage of the product, which if exposed to air will eventually support microbial growth which can then track back into the main container causing spoilage. i.e. fermentation or mould growth.
- In most cases upon request, we can provide a coupling (shown in below images) whcih can connect to the plastic valve and allow a stainless valve to be coupled directly.
- The picture below shows additional options:
Cleaning
- All hose attachments and pipe work used for dispense must be subject to thorough cleaning and disinfection in-line with standard hygienic practices before attachment to the Hybrid.
Hose CIP
- It is vitally important that full consideration is given to Hygienic practices when coupling lines to the Hybrid, as contamination at this point will reduce the shelf-life of the product. A contact surface spray sanitizer should be employed on the hose coupling and on the exposed area of the valve prior to final connection.
- Where there is a requirement for a valve, hose or associated pipe work to be fitted you must remember that this requires to be supported independently. The Integrated valve that you are connecting to is attached to the polythene liner and this is not designed to support additional weight.
- We recommend hat once IBC is connected to the system it is dispensed fully within 4 weeks.
Using Valves
- When dosing into a pressurised system a non-return valve must be installed between the dosing pump and the high pressure line. We would recommend that this is fitted even when it is a positive displacement dosing pump. Unpasteurised beer or liquor will contaminate the sterile product if it flows back to the Hybrid.
- Avoid the use of intermediary tanks especially if they are open to atmosphere as this will become a contamination risk. The bags are designed to collapse and do not require an intermediary tank. If this cannot be avoided then cleaning procedures must be put in place to insure that product is not left in the tank for any longer than 24hrs.
- Caution is advised when dosing immediately in front of the filter. The product must have sufficient turbulent flow to dissolve and mix with your beer/product prior to reaching the filter. Otherwise the extract will reach the filter medium in a concentrated state and could be filtered out (loss of utilisation) or blind the filter bed (poor filtration performance). A suitable in line mixer is advisable or injection prior to a “chiller” heat exchanger or equivalent where sufficient turbulence will occur.
- Remember when the product is cold the viscosity will increase, and flow can be reduced through any pipework prior to a pump. Therefore, the dosing pump should be positioned close to the container. It is also advisable to create a head if possible by raising the container well above the pump.
- Avoid small bore pipework between the container and the pump inlet (2” or 50mm preferable). It may require a positive displacement pump such as a lobe or a peristaltic pump to overcome any of these issues if compromised.
Shelf Life
- Please remember these products are only micro-biologically stable due to the controlled conditions in which they have been packed. Once these controlled conditions have been breached there is a risk of microbiological spoilage.
- We advise:-
- A maximum of 4 weeks after opening if the product is stored at refrigerated temperatures below 5 °C
- A maximum of 1 week after opening if the product is stored at ambient temperatures 5-30 °C
- If the product is exposed to the environment either by decanting into another container or opening the bag and allowing air it then should be used within 48 hours.